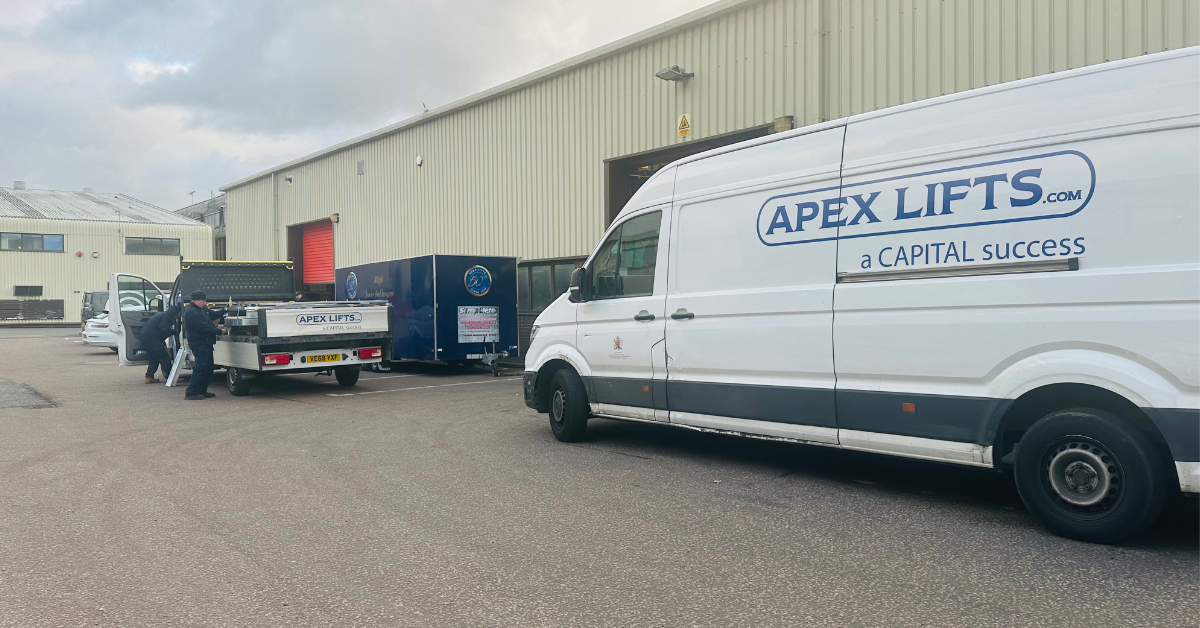
In December 2024, our workshop in Sidcup underwent significant upgrades, including the addition of a pad sander and enhancements to the brake press. These upgrades will deliver faster turnaround times, maintain our already high product quality, and improve customer service.
The Pad Sander
This new tool helps clean up lift parts and remove burrs from engraved areas. With it, we’ve established a new Engraving Department within the workshop.
This department specialises in engraving various metal parts, reducing downtime, and speeding up delivery times for custom components.
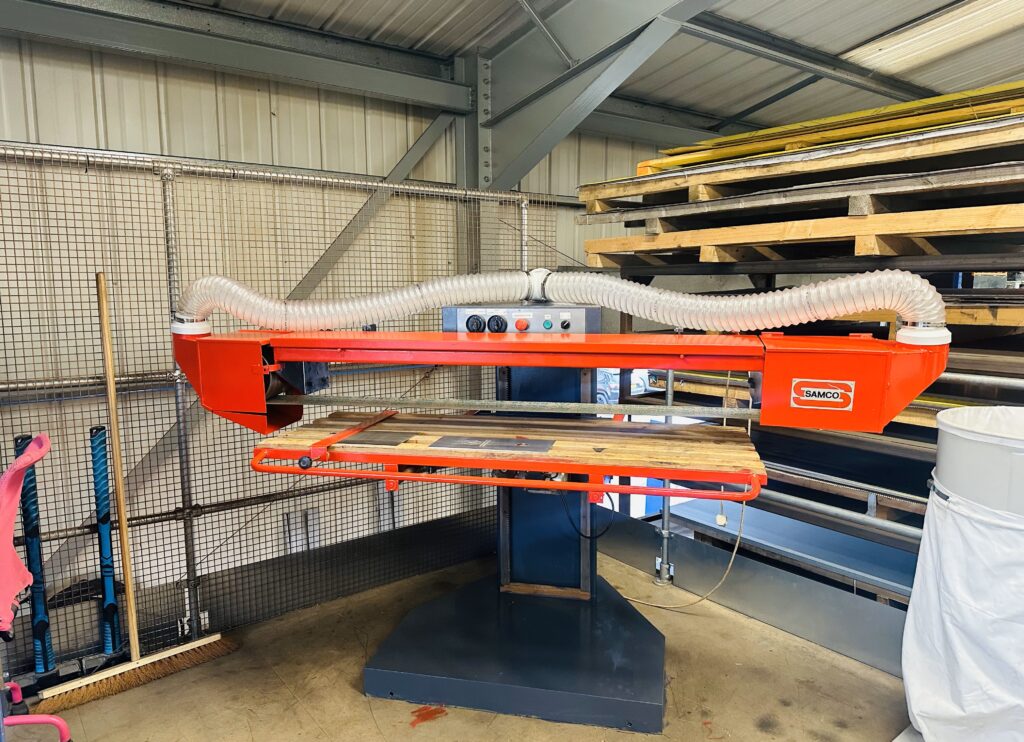
Pad Sander
The Brake Press (Folding Machine)
The brake press is used to fold and bend sheet metal and plates, the brake press allows us to create bespoke lift designs tailored to specific customer needs. It clamps metal between a punch and a die, shaping it into precise angles and forms. This capability enables us to customise designs with efficiency and accuracy.
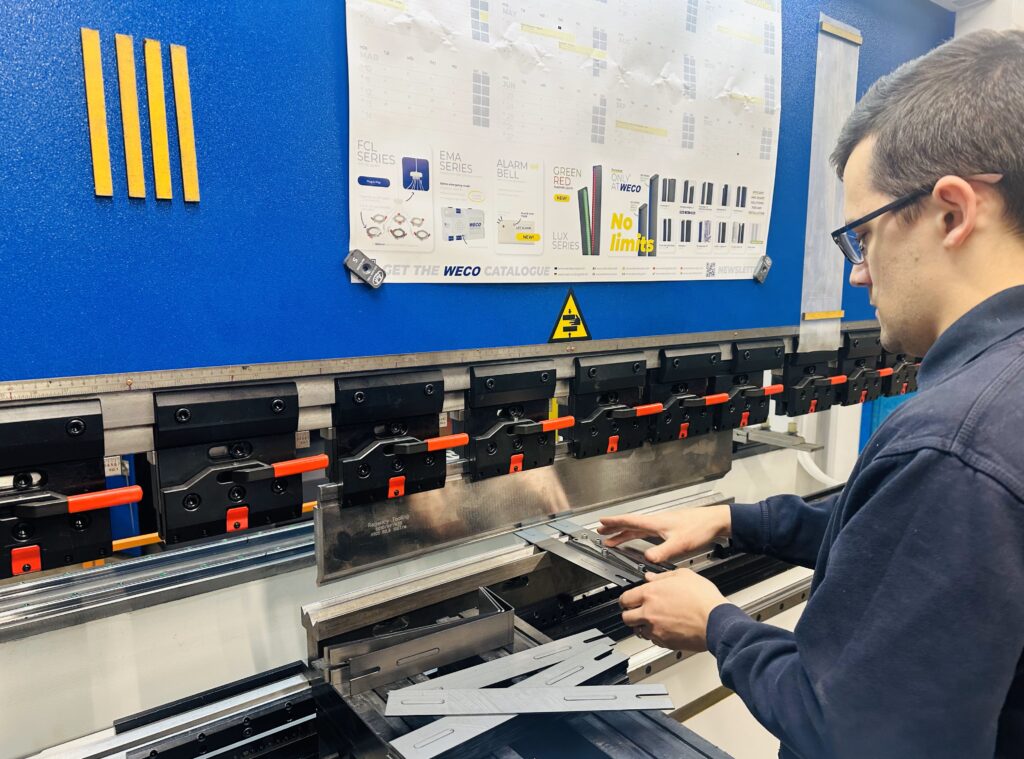
Brake press
The hydraulic-system brake press is built to CE safety standards, featuring components such as electric safety switches and safety controllers. This ensures that health and safety remain a top priority in our operations.
Our workshop upgrades are customer-focused
The improvements to Apex workshop are designed to enhance quality and ensure we stay ahead in the lift industry. With the latest technology in place, we can explore new manufacturing possibilities, further benefiting our customers.
Alan Simons, Workshop Manager, said:
“Our workshop has seen significant investment recently, which will have a positive impact on both the company and our customers. These upgrades will help us boost delivery times, maintain high product quality, and improve customer satisfaction.”