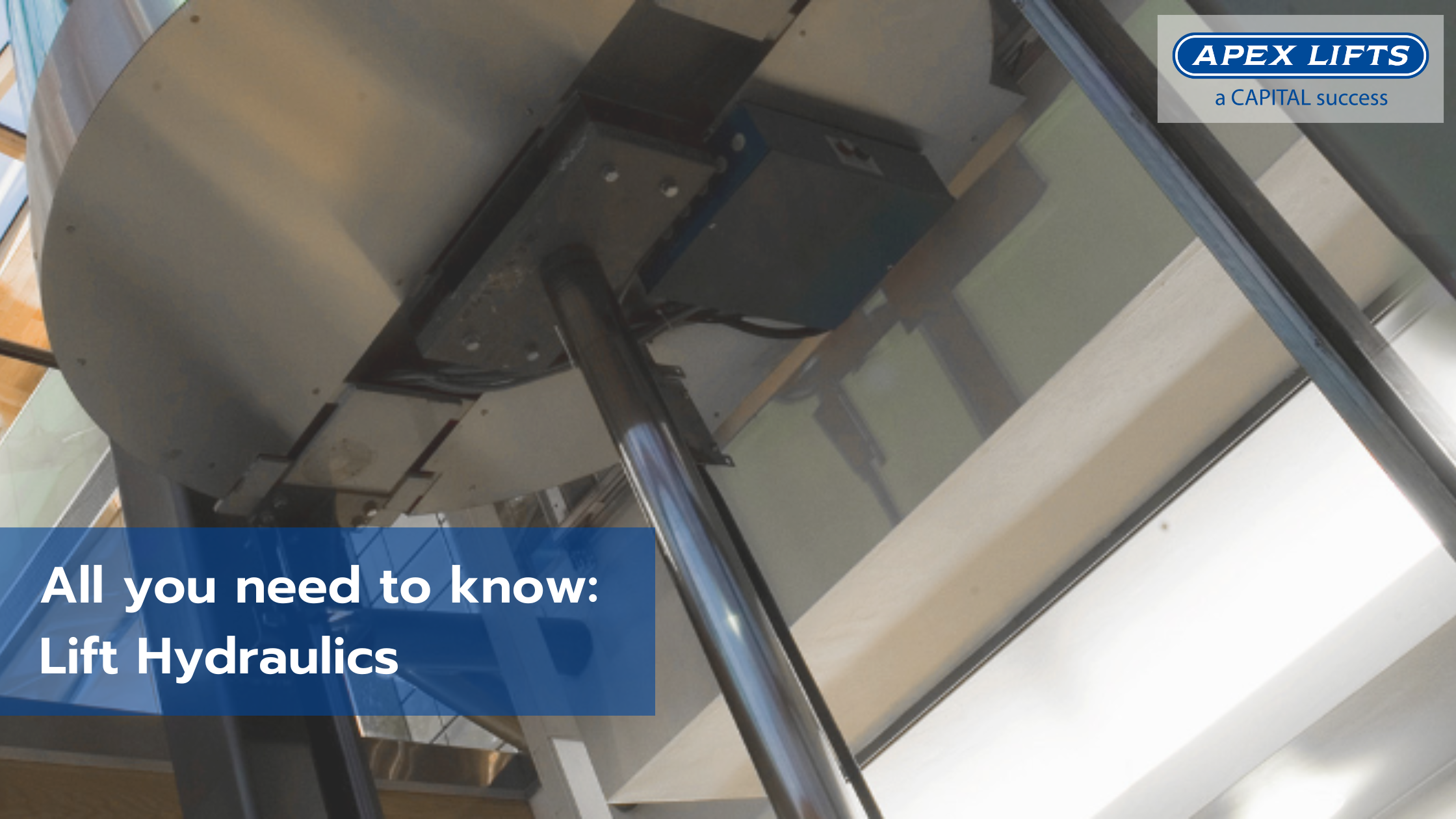
Hydraulic lifts are a popular choice of lift system used all over the world and can be located in a range of public and private buildings. Hydraulic systems are in fact used in a range of daily tasks such as your car’s braking system. It is the basic principle behind hydraulics that provide continuity and as such hydraulic lifts are no different. There are five main components to a hydraulic lift that will be found universally, beginning with a piston inside of a cylinder (ram), a pump, a motor, an oil reservoir tank, and a valve.
Typically, hydraulic lifts have a separate machine room, to which the motor, pump, and fluid are homed. This can often take up more space than expected, as opposed to a machine-room-less (MRL) hydraulic lift. The difference being, that MRL hydraulic lifts house the large machinery components within the shaft, creating a far greater space-saving option for smaller areas.
Although the theory behind hydraulics may seem complicated, it is far simpler than one may think. It is based on the fundamental principle that when traveling upwards, the pump forces oil inside of the cylinder, which in turn forces the piston to push the lift car up. In turn, meaning that to travel back downwards the valve must open to allow the oil to run back down to the reservoir.
Put simply, once the valve is closed oil can only travel from the reservoir to the cylinder, and when the valve is reopened the oil can then only travel from the cylinder to the reservoir. It is the lift car’s control that then operates the pump to which moves the oil. It is only when a floor is reached that the pump is then switched off, in which the lift car then remains on top of the piston, held in place by the trapped oil within the cylinder.
The process of choosing the right lift for you can be a very trying time, as such, this blog aims to provide you with some simple and honest pros and cons. There are various limitations and benefits to hydraulics and as such should be determined on factors such as the space, travel height, and frequency of use of the lift.
Initially, a large benefit of a hydraulic lift is the cost. Often this type of lift can provide better value for money than for example a traction lift. However, in the long run, your hydraulic lift could end up costing you more as they are known to not be as energy efficient. Especially if you are scoping to meet BREEAM efficiency ratings. This is more so to do with the fact that hydraulic lifts require a lot of power to move the lift car making its energy usage incredibly higher than when compared to a traction lift which is balanced using a counterweight.
In instances where you find yourself held for space above the shaft, a hydraulic lift with a separate machine room can be a great idea to provide you with vertical transportation. However, this too can be a limitation as you require far more ground space to room the machinery and oil pit than an MRL lift. Which may not always be suitable for every type of building due to floor space often coming at a premium.
Some may also take into consideration the safety element of a hydraulic lift, as with the lift being cableless, it is near on impossible for a dead drop scenario. In fact, a hydraulic lift is only capable of falling in line with the speed of an oil leak. Although largely a positive with its increased safety, the oil leak in itself can be a hindrance to the lift’s general health and should be thoroughly considered prior to installation, as well as the significant risk an oil leak poses to the environment. This however is easily preventable as with any lift through proper care and maintenance, pre, during, and post-installation.